

To authenticate the results, the presented method was validated with experimental data from two different flight test programs, three small-scale wind tunnel tests and one full-scale wind tunnel test. This approach made it possible to take into consideration blade deformations in simulations and revealed the high influence of aeroelastic effects on rotor loads and performance at hover conditions. The method used combines a high fidelity Navier-Stokes aerodynamic model coupled with a low-order beam structural model. Additionally, it aims to validate a new computational method based on a set of experimental results for a UH-60A helicopter rotor.
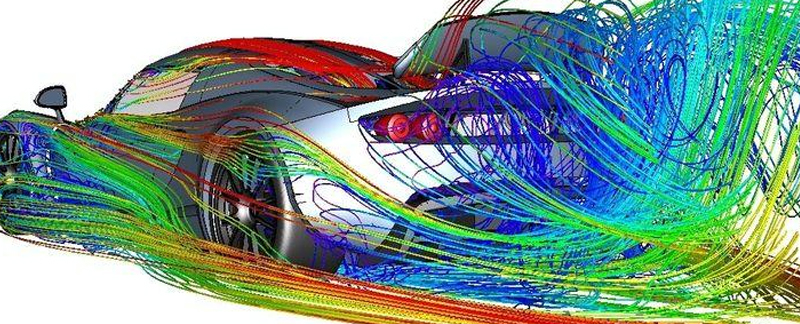
The purpose of the presented work is to indicate the possible influence of blades elasticity on helicopter rotor. In existing literature the effects of an aircraft structural deformation on airloads distribution and performance are fairly well described but mainly for airplanes. The paper deals with the numerical analysis of a helicopter rotor in hover conditions, including aeroelastic effects. This comparison proves rational of using virtual disk to replace real propeller in the CFD simulation. Moreover, the results of thrust from each propeller from simulation are compared to that of analytical BET method and that of propeller performance provided by the manufacturer. The aerodynamic forces and the dynamic fields surrounding the tri-copter will be discussed in detail, while the effect of tri-copter’s frame on rotor operation will also be considered. A steady, incompressible solver with k-ω SST turbulence model is applied in the simple Foam algorithm.
ANSYS FLUENT VBM CODE
Finally, after obtaining the relative angle of -2 degree between the rotor tip-path-plane and the tri-copter’s frame, the simulation for the tri-copter in forward flight including three rotor disks rotating at 4732-RPM will be carried out through the rotorDisksource library of the open source code OpenFOAM. Secondly, these force coefficients are exploited in the analytical approach based on the Blade Element Theory (BET) to determine the rotor disk plane angle and the tri-copter’s frame angle for steady, level, forward flight at 15-m/s. In the first part, the aerodynamic performance of the tri-copter’s frame (not including the propellers) is investigated at the range of angle of attack from -12 degree to 12 degree by simulation in OpenFOAM. Its propulsion system consists of three two-blade propellers typed XOAR PJP-T-L 1245 with12-inch diameter and 4.5-inch pitch. The tri-copter has 0.75-meter radius and 15-Newton weight. This paper presents the process of implementing numerical simulation for a tri-copter in forward flight using the open source code OpenFOAM with the library of Virtual Blade Model (VBM). It could be used successfully in helicopter rotor blades design process. The presented aeroelastic helicopter rotor model combines all advantages of using three-dimensional Navier-Stokes solver with relatively low computational costs and high accuracy, confirmed by wind tunnel tests. The comparisons showed very good agreement of the data in most of the analyzed cases and pointed out new research possibilities. The results of calculations were compared with experimental data for a hover state and a forward flight with three different flight velocities. The accuracy of created module was validated with wind tunnel tests data of IS-2 helicopter rotor model, performed in Institute of Aviation. The dedicated structural dynamics solver, based on equivalent beam model of a blade and Finite Difference Method, was developed and coupled with CFD part using User Defined Functions in Fluent software. This connection guarantees exceptional capabilities and fidelity in comparison with simulation time. It uses the well-known Navier-Stokes equations aerodynamic solver - ANSYS Fluent, and modified Virtual Blade Model (based on Blade Element Theory) for rotor flow calculation. The paper presents a new efficient methodology for calculating helicopter rotor loads, deformations and performance.

Complex Fluid Structure Interaction models are excellent tools for validation purposes, but the design process requires simpler models with lower computational cost and still relatively high accuracy and capabilities.

However, the computational cost of this type of simulation is usually very high and for this reason it cannot be used in interactive design process or optimization run. Sophisticated computational fluid dynamics and structural dynamics models, available on the market, coupled together enable such analysis with very high fidelity. Modern helicopter rotor blades design requires taking into account complex aeroelastic phenomena.
